Линия нанесения комплексного трёхслойного покрытия PRIMA ART
В 2018 году компанией «ЛАДА-ФЛЕКТ» была запущена высокотехнологичная линия комплексного трехслойного покрытия PRIMA ART, позволяющая наносить на металлические поверхности покрытие, стойкое к воздействию агрессивных сред.
Класс коррозионной стойкости покрытия — С-5М, что подтверждается испытаниями в камере солевого тумана в течении 2000 часов. Долговечность покрытия более 20 лет в условиях высокой коррозионности атмосферы, например, в морском климате.
Линия PRIMA ART включает в себя: 11 ванн с реагентами, 1 печь для сушки катафорезного грунта, 1 печь для полимеризации поверхности и 2 камеры для нанесения электроосаждаемой полимерной краски.
Цветовая палитра комплексного трехслойного покрытия соответствует международному стандарту по системе RAL. Цвет покрытия выбирается заказчиком.
Длина конвейерной линии
400 м
Максимальный размер окрашиваемых деталей
2000×2000×2000 мм
Технология нанесения покрытия
Перед поступлением изделия из металла на линию PRIMA ART производится удаление (при необходимости) остатков застаревшей краски, грязи и пыли под воздействием воздушно-абразивной струи.
Этапы на линии PRIMA ART:
- Подготовка поверхности деталей
- Нанесение циркониевого покрытия.
- Нанесение катафорезного покрытия.
- Нанесение полимерной краски.
Получаемое комплексное трехслойное покрытие
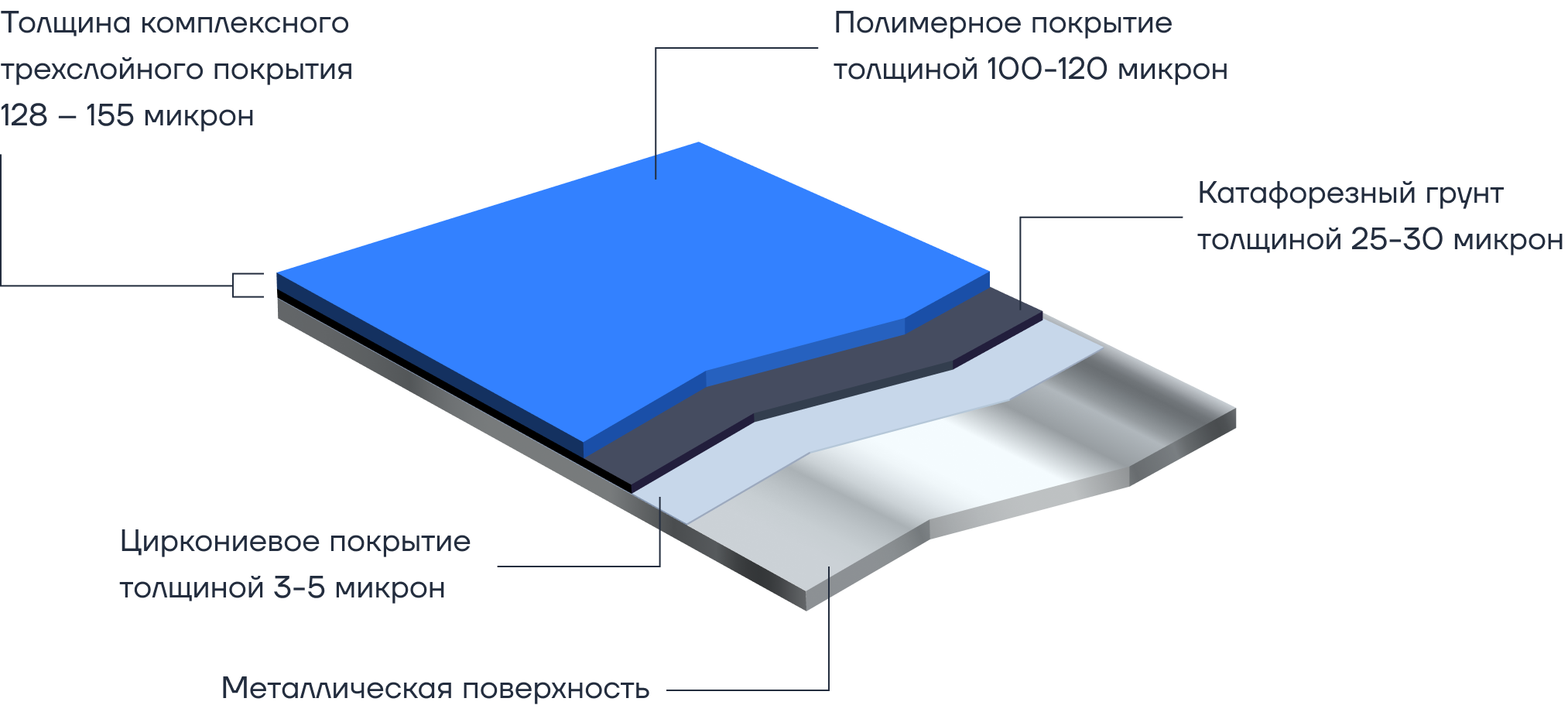
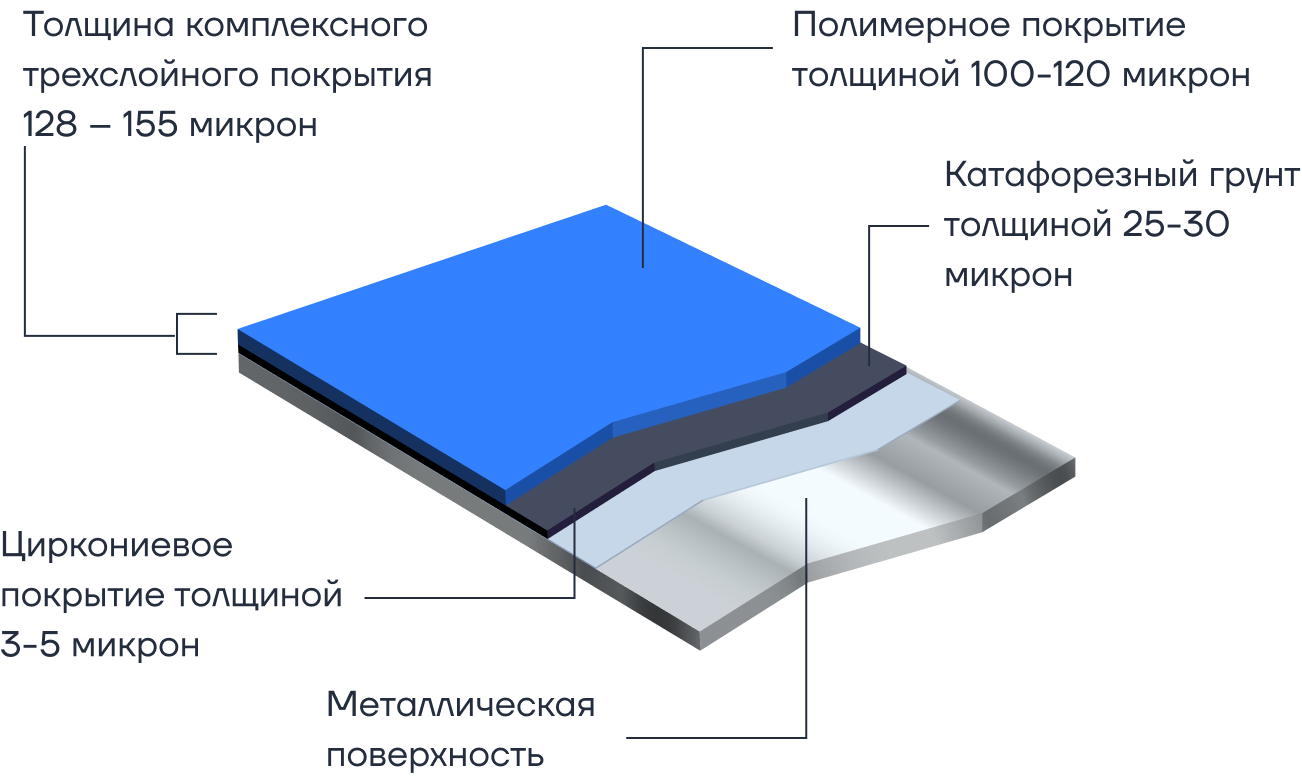
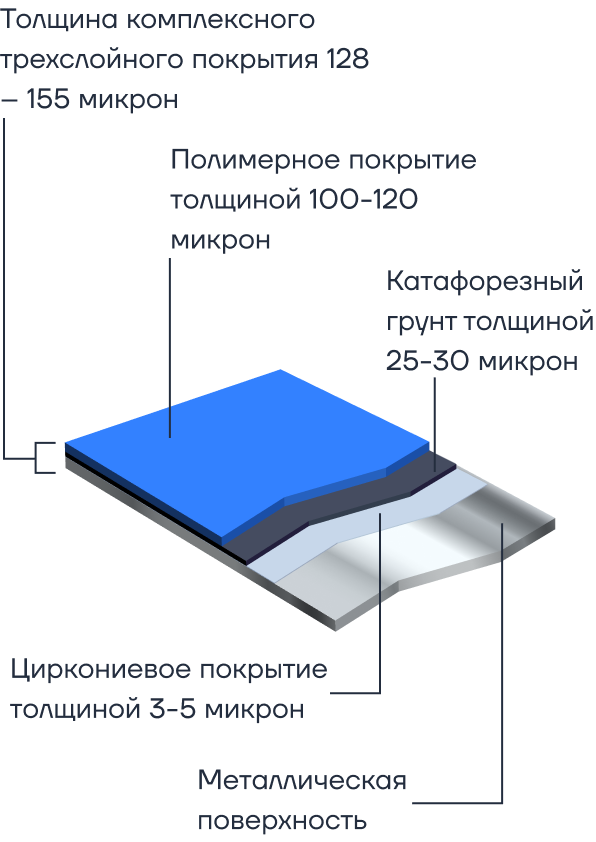
1 этап. Подготовка поверхности
Производится подготовка поверхности детали в семи ваннах с активными реагентами, в которых удаляется грязь, пыль, масла и поверхностная коррозия. По окончании очистки остатки растворов смываются деминерализованной водой.
2 этап. Циркониевое покрытие
Нанесение циркониевого покрытия — это один из этапов антикоррозийной обработки поверхности детали.
Цирконий насыщает поверхность электронами, восстанавливает кристаллическую решетку верхнего слоя детали, которая повреждается при термической и механической обработке. Наличие свободных электронов на поверхности металла улучшает адгезию со следующим слоем покрытия — катафорезным грунтом.
Толщина циркониевого покрытия
3-5 микрон
3 этап. Катафорезное покрытие
Нанесение катафорезного покрытия — этап грунтования изделия из металла для защиты от образования ржавчины. Покрытие обладает высокой прочностью и износостойкостью за счет проникновения в труднодоступные места, грани и поры.
Выполнив на первом этапе очистку от ржавчины, в дальнейшем можно забыть о рисках подобного поражения изделия, находящегося в среде с высокой относительной влажностью и с содержанием морской соли.
Технология нанесения покрытия — деталь погружается в ванну с коллоидными (жирными) растворами, при подаче напряжения осуществляется заряд катафорезного грунта с последующим формированием защитного слоя. Перед сушкой катафорезного грунта деталь проходит ванну с ультрафиолетом. Сушка производится в печи при температуре от 140 до 200 °С.
Равномерность полученного катафорезного покрытия на плоскости и острых кромках колеблется в пределах от 25 до 45 микрон.
Равномерность катафорезного покрытия
25-45 микрон
Сушка при температуре
140-200 °С
4 этап. Полимерное покрытие
Применяемые типы красок: полиуретан, полиэфир, эпоксиполиэфир, полиэтилен.
Технология нанесения покрытия — полимерная краска наносится методом электростатического осаждения в покрасочной камере. Полимеризация электроосаждаемой краски происходит в печи при температуре от 140 до 200 °С.
Получаемое полимерное покрытие обладает коррозионной стойкостью и придает изделию декоративный внешний вид.
Толщина полимерного покрытия на плоскости и острых кромках колеблется в пределах от 100-120 микрон.
Толщина полимерного покрытия
100-120 микрон
Система управления
Контроль качества
Чистое и бережливое производство
Особой гордостью является борьба за чистоту окружающей среды и сведение к минимуму вредных отходов производства. На нашем производстве имеется цех очистки воды после ее прохождения через покрасочный цех с агрессивными реагентами. Вода доводится до питьевого качества и только после этого частично используется в технологическом процессе, а частично сбрасывается в систему канализации.
Камеры сушки и запекания оснащены системой рекуперации тепла.
Горячий воздух из камеры сушки по системе воздуховодов направляется в камеру запекания, где донагревается до нужной температуры.
Горячий воздух из камеры запекания по системе воздуховодов проходит через водяные теплообменники, где происходит нагрев воды, которая используется в технологическом процессе.
Термический дожигатель, установленный в камерах сушки и смешения, работает под избыточным давлением, что позволяет дожигать угарный газ и растворители и минимизировать количество вредных выбросов в окружающую среду.
Вокруг покрасочных камер в полу проложена токоотводящая медная проволока для защиты оператора от накопленного статического электричества.
Аналогов данной системы на территории РФ в гражданской промышленности нет.
Результаты испытаний на коррозионную стойкость
Коррозионные испытания на стойкость комплексного трехслойного покрытия проводились в камере соляного (морского) тумана, после которых был определен срок службы изделий из металла с этим покрытием.
Образцы находились в соляном тумане в течении 2000 часов без образования видимых повреждений. Комплексное трехслойное покрытие не входит в химическую реакцию с агрессивной средой, сдерживает появление ржавчины.
Коррозийная стойкость покрытия в камере соляного тумана
2000 ч.
без видимых повреждений
Результат испытаний по ISO 12944 в течении 2000 часов:
- Распространение коррозии от надреза — менее 1 мм;
- Образование пузырей на поверхности — 0 (S0);
- Образование коррозии на поверхности — 0 (SO)
- Адгезия — GT0 (100% сохранность)
Результат испытаний по ISO 4628 в течении 2000 часов:
- Распространение коррозии от надреза - менее 2 мм;
- Образование пузырей на поверхности – 0 (S0);
- Образование коррозии на поверхности – Ri 0